Fielding 3D Printing to Enhance the 173rd Airborne Brigade’s Readiness
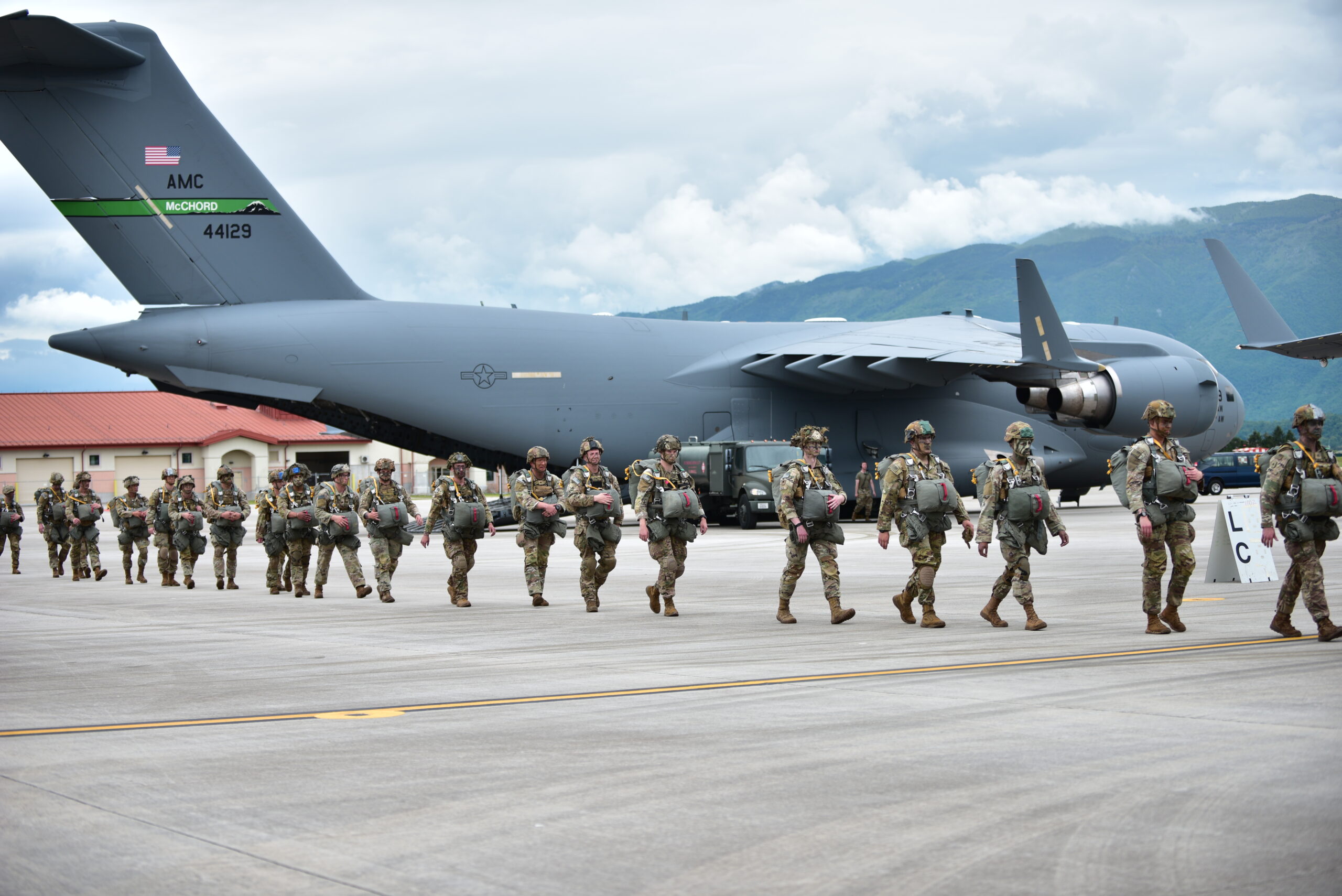
The US Army’s 173rd Airborne Brigade should field expeditionary three-dimensional (3D) printing capabilities to increase its combat readiness. As the Army’s contingency response force in Europe, the 173rd Airborne Brigade’s ability to innovate and rapidly deploy are crucial for supporting US military operations in Europe, Africa, and Central Command. The Army should equip the brigade with large-scale, deployable metal and plastic printers. Doing so will enable swift tactical solutions and serve as a model for the Army’s modernization efforts in preparation for future conflicts.
Leveraging Initial Success
Though nascent, the Army is prioritizing additive manufacturing in combat in preparation for large-scale conflicts. The Army recognized the benefits of 3D printing with the launch of the Advanced Manufacturing Center of Excellence (AM CoE) in 2019. In 2024, the AM CoE built the world’s largest hybrid additive and subtractive apparatus, the Jointless Hull, capable of printing an entire M1 Abrams tank. Additionally, Additive Manufacturing Research estimates the DoD will grow its 3D printing budget from $0.3 billion in 2023 to $1.8 billion by 2032. Lt. Gen. Christopher Mohan, AMC’s acting commander, emphasizes the “growth requirements coming primarily out of units in Europe.”
In Europe, the 173rd Airborne Brigade began 3D modeling to print spare parts near the front lines. The Brigade Support Battalion uses the Raise3D Pro2 and MakerGear Ultra One while the brigade’s innovation team employs the Prusa Mk4S 3D printer. Recognizing the benefits, the brigade appointed an innovation officer and is acquiring two more printers to test and validate functionality for its Unmanned Aerial Systems (UAS). To build on this success, the brigade should procure containerized, large-scale 3D printers capable of operating in austere environments.
3D Printer-Material Analysis
A key cost driver in additive manufacturing is the decision to use either metal or polymer. Metal prints are more durable, resistant to weather, chemicals, and impact, and offer diverse material properties. However, some polymers can compete with metals in corrosion resistance and strength, making them ideal for prototyping due to their lighter weight (60-70% lighter than aluminum). The brigade should prioritize deployability, functionality, volume, speed, and cost when deciding on which direction to go. Until dual-capable printers are available, the brigade should buy both types, prioritizing large-scale metal printers at the brigade level and small-volume polymer printers at the battalion level.
The printer and accessories are only a fraction of the total cost of additive manufacturing. Additional expenses include maintenance, filament, and software subscriptions. The value of metal 3D printing relies on its impact and return on investment, calculated by comparing acquisition costs (ranging from $150k to over $1M) to savings. For instance, Shukla Medical projected their Markforged Metal X to pay for itself in under two years by in-sourcing prototyping. The system, costing $150k-$175k, would save $1,000 per prototype with 10 units per month, leading to $10k in monthly savings and breakeven in about 18 months. The 173rd Airborne Brigade also subscribes to SOLIDWORKS 3D CAD and Shapr3D for its Prusa 3D printers. To offset these costs, the brigade should seek designation as a test and fielding force under the Army’s 15-year, $4.5 billion modernization plan.
173rd Airborne Brigade is Ideal for Field Testing
173rd Airborne Brigade is the optimal unit for field testing containerized deployable 3D printers. This unit is ideal because 3D printing could save money and time for international shipments, introduce possible R&D opportunities with NATO militaries, and enhance combat lethality as a contingency response force. For example, in 2017, Soldiers in South Korea identified a fire-suppression cap fault that rendered their Mine-Resistant Ambush Protected (MRAP) vehicles non-mission capable. To avoid the estimated five-month delivery wait for replacement parts, they 3D-printed the 284 needed replacement caps. Lt. Gen. Aundre Piggee, the Army G-4 at the time, noted that, “it was only a small cap that was the issue, and we 3D printed a fix for it. Just 1,472 non-mission-capable days saved – for about $2.50 per part.” This highlights how 3D printing might help the 173rd Airborne Brigade maintain a higher rate of readiness just by reducing international shipping costs and reducing non-mission-capable readiness days through on-the-spot-manufacturing.
Furthermore, industrial-sized printers could support lightweight maneuverability and promote collaboration between NATO partners. In 2017, The Automated Construction of Expeditionary Structures (ACES) demonstrated the flexibility of expeditionary printers, by successfully printing a 512 square-foot concrete structure. ACES reduced construction materials by half and reduced manpower by 62% compared to traditional plywood structures. This is advantageous for the 173rd Airborne Brigade because it is expected to rapidly deploy to locations of questionable security with only mission-essential equipment. The ability to deploy and then identify which type of structure or tool best suits the brigade’s materiel requirements enables greater speed and flexibility maintaining readiness. Additionally, 3D printing presents an opportunity for the 173rd Airborne Brigade to further interconnect with NATO members through information sharing. Recently, the British Army showcased their additive manufacturing capabilities by printing metal and plastic spare parts in under an hour during the Steadfast Defender NATO Exercise. Their software also enables information sharing amongst NATO members. The 173rd Airborne Brigade should field test 3D printers, ensuring the US Army remains a leader in militarized technology, fostering greater collaboration and interoperability within NATO.
Fielding 3D Printers into the Formation
The US Army aims to equip Soldiers with 3D printing tools to address tactical challenges. This initiative connects depots, arsenals, plants, and Soldiers through a digital archive of approved 3D designs. In 2012, the Army tested this concept using the Army’s Rapid Equipping Force (REF), which deployed two 20-foot mobile Expeditionary Labs. Each lab included a Stratasys Fortus 250mc printer and communications systems linking forward teams to REF headquarters. REF also supported the ARDEC initiative by digitally sharing 3D blueprints with other services. In 2020, Gen. Gus Perna, the head of Army Materiel Command, emphasized the need for on-the-ground 3D printers to address “readiness drivers” – frequent breakdowns of critical equipment. He clarified that additive manufacturing would complement, not replace, traditional supply chains, aiming to enhance battlefield readiness.
The 173rd Airborne Brigade should field either the Spee3D or xCell for expeditionary 3D modeling. The Australian-made Spee3D WarpSPEED3D printer is the best option because it is battle tested by Ukraine, energy-efficient, deployable, and rapidly prints large parts. The Spee3D is already being tested in Ukraine’s battlefield since 2023, where seven WarpSPEED3D metal additive printers were donated. Its cold spray additive technique is ideal for combat because it does not require lasers or gases. Additionally, the WarpSpee3D is expedient, energy-efficient, and produce parts up to one meter in diameter or 40kg, with a manufacturing rate of 100g per minute. For example, the company printed a 4.5-pound aluminum bronze gunner’s ratchet in 60 minutes. The machine is user-friendly with on-screen instructions and Spee3D offers a 15-day training program. Most importantly, this 3D printer is highly deployable as Calum Stewart, Spee3D’s Director of Defense Programs, stated, “you can pick it up, put it in the back of a truck, put it down, set it up, and have it up and running in 45 minutes.”
The second-best option for the 173rd Airborne Brigade to field test is the xCell. This American-made, semi-automated, expeditionary system specializes in producing high volumes of UAS and spare parts. Notably, the xCell can assemble a drone in under 24 hours. Firestorm Labs currently offers two container models – 20ft and 40ft. While still in development, the xCell is a viable option, especially since Firestorm Labs is financially backed by Lockheed Martin. Its deployability and focus on UAS printing make the xCell a strong fit for the 173rd Airborne Brigade’s needs.
Leading from the Front
As 3D printing becomes more affordable and accessible, new security risks may emerge. In 2021, a Pentagon watchdog published a report exposing the cybersecurity threats residing in the DoD additive manufacturing programs. The report discussed concerns that an adversary could compromise a service’s 3D printing design data to re-create and use this information for the enemy’s advantage. In 2016, RAND Corporation demonstrated this cybersecurity threat when university researchers hacked a 3D printing system, altering drone propeller code. The printed propeller appeared perfect, yet microscopic faults in its blade produced failure, revealing risks as additive manufacturing could print mission essential parts like helicopter engine components. If fielded containerized 3D printers, the 173rd Airborne Brigade should take a holistic approach to hardening its 3D printing software against cybersecurity threats.
The 173rd Airborne Brigade should lead NATO’s tactical containerized 3D printing efforts. In the end, the benefits of additive manufacturing far outweigh the costs. As the battlefield evolves, 3D printing offers immediate value to the Brigade. The Army should prioritize the 173rd Airborne Brigade in its long-term fielding plan, leveraging the Brigade’s leadership in innovation to address key challenges such as certification, safety, intellectual property, and compression of need-to-solution timeline.
Disclaimer: The views expressed are those of the authors and do not reflect the official position of the 173rd Airborne Brigade, Department of the Army, or Department of Defense.